Here are some of our customers. We have worked with large groups and SMEs, very diverse sectors, in different countries, with some we have spent months training and with others only a few days, but they have one thing in common: with all of them we have shared our experience and we have learned from each of them.
Next customers
If you answered "no" to any of these questions, you might be our next customer!
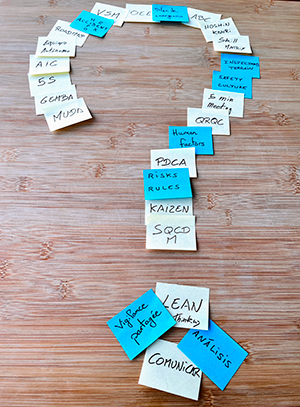
- Have I defined my SQCDM control KPIs and do I know their trend? Do I hold improvement meetings if indicator results are off target?
- Do I understand the philosophy of Lean thinking and its tools? Is there a person in charge of continuous improvement in the company?
- Have I identified bottlenecks and major flow issues? Is there a medium-term action plan?
- Do I know my OEE?
- Do I know what is the MUDA (non-added value activity) that makes me less efficient?
- Do I have standardised and updated processes?
- Is there visual management in my company?
- Do I have an organisation of autonomous teams in production? Is there a team board showing the team situation in real time on the shop-floor?
- Do I measure the flexibility of my teams using a versatility matrix and do I have an associated training plan?
- Do 5-minute meetings take place in the teams before the start of the shift? Do I have "cascading" meetings?
- Do I regularly carry out Kaizen (improvement groups) in which the majority of employees participate?
- Do I have a system in place to determine the root causes of problems? Are my employees trained in problem solving tools?
- Do managers perform regular Gemba Walks (safety audits, workplace audits, or other type of inspections)?
- Is there a preventive maintenance schedule for the machines and is it respected?
- Do I know the frequency rate of my company and can I explain the reason for my results?
- Have the "life saving rules" associated with the major risks of the company been defined?
- Is there a culture of prevention in my company?
- Do my teams apply shared vigilance?
- Do I know human factors and how to use them to improve safe behaviour?
- Do I have a job induction plan and does it start with the safety aspects?
- Has a risk analysis been carried out for each workstation on the shop-floor?
- Are Planned General Inspections carried out periodically on the shop-floor?
- Each time an accident (or near-miss with high potential of loss) occurs in my company, is it analysed?
- Have I defined an emergency plan? Is there a crisis management procedure?
- Is there a follow-up of the activities of external companies (contractors) in terms of safety?
- Are periodic prevention training sessions organised to raise employee awareness of the risks?
- Do I frequently share with the employees the situation of the company, the projects, the difficulties, etc.?
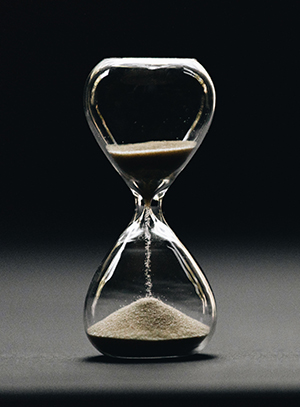