Ensuring that all of our employees return home safe and sound at the end of the working day is a duty of every employer. But the risks cannot always be eliminated, sometimes you just have to “minimise” them. And sooner or later, people make mistakes that can have serious consequences.
To be able to work in a safe environment, you must rely on:
- concrete and effective prevention activities
- shared vigilance, we all take care of each other
- training and human factors, to avoid errors
- best practices on the shop-floor, application of continuous improvement methodologies
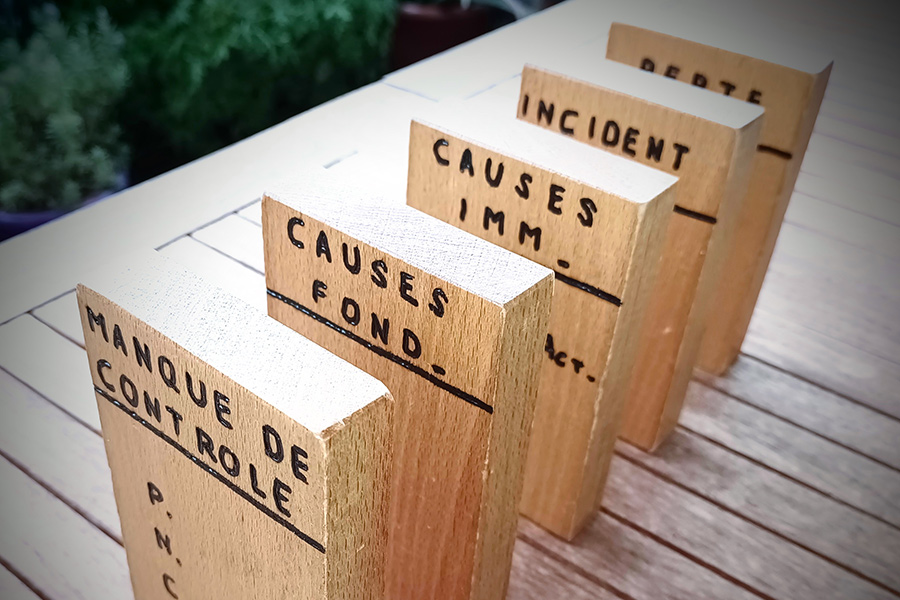
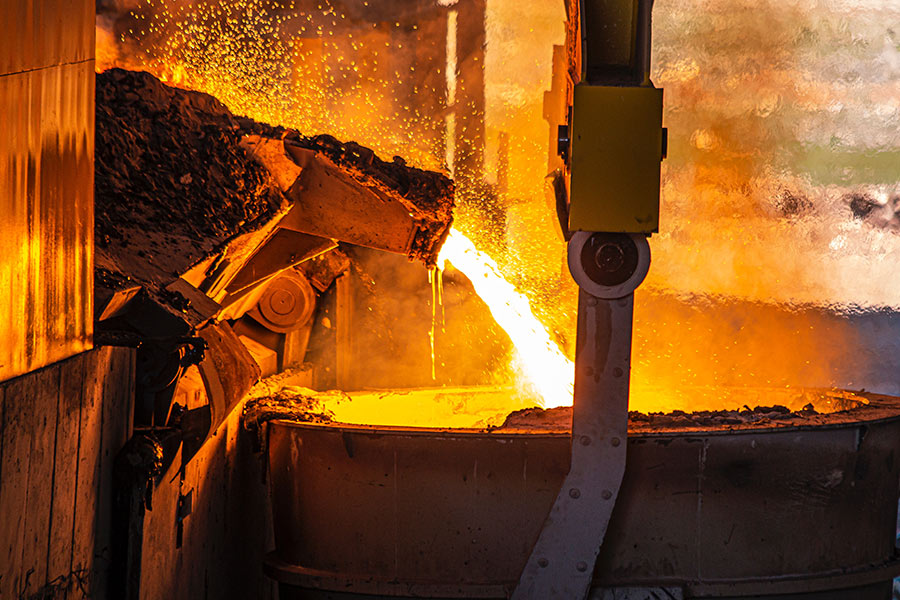
How can we help you?
- carry out an assessment of the main risks to create an action plan focused on achieving zero severe accidents
- support you on specific topics such as:
- creation and implementation of a health & safety management system
- crisis management after a severe accident
- accidents/incidents analysis (REX)
- change management to create a prevention culture
If we talk about: | The tools & method we can apply are: |
General | HSE – Day-to-day Safety management / Concepts & commitment |
Basics | PPE / Team meetings / HSE promotion |
Evaluation | Risk assessment (HIRA, FMEA, What If) |
Analysis | Accidents analysis (RCA, Causes & effects, Dominos, Fault Tree Analysis) / Ergonomics / Critical tasks analysis / Shop-floor inspections / Worksites review |
Measures | KPIs / prevention rate / management systems audits |
Systems & roadmaps | Comprehensive audits = 1. Questionnaire 2. Shop-floor inspections 3. Employees interviews 4. Report / Adapted referential / OHSAS18001, ISO45001, ISRS, MASE, ISO14001 |
Improvement | Workstations audits |
Motivation | The human factors & behaviours (Mechanism of human errors, motivation & commitment) / Shared vigilance / Competences matrix / Wellbeing (QLW-Quality of Life at Work) / Change management |